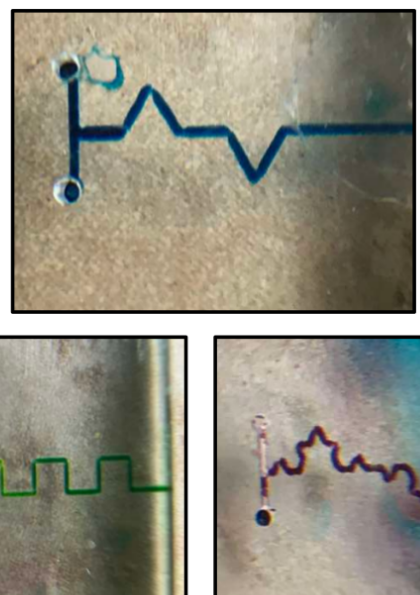
Lasers are used in material processing industries for various applications, including (but not limited to) cutting, engraving, welding, bending, surface texturing, annealing, surface hardening, cleaning and polishing. Lasers offer the distinct advantage in material processing of not using any physical cutting tool. Instead, a chunk of monochromatic and coherent photons strike the surface to ablate/heat the material either by heating cycle (i.e photo ablation) or by breaking of atomic bonds (i.e. cold ablation). The absence of physical cutting tools also eliminates the requirement of work holding devices, known as fixtures, resulting in significant savings of cost and time.
Compared to other manufacturing processes, lasers consume less time, energy and manpower. An entire process can be automated easily, which makes laser an integral part of Industry 4.0.
In the last decade, laser micromachining has evolved as a potential fabrication process for many microfluidic applications on different material substrates like glass, polymers, silicon and metals. With the availability of short and ultra-short pulse lasers, sub micro-meter features can be created over the surfaces without producing any physical defect. Femtosecond and picosecond lasers can create structures inside a material without disturbing the upper layer. A variety of complex structures including 2D and 3D can be rapidly created over any surface.
Lasers can precisely etch metals and polymers with submicron accuracy. The precision depends upon the type of laser beam and its focal diameter. Theoretically, the beam diameter can be reduced to the wavelength of the laser beam but in actual conditions and because of imperfect optics, the beam diameter will normally vary from 10 to 100 times of beam wavelength.
Most of the industries today employ a fibre laser and a CO2 laser for cutting of metals and organic materials respectively. The low-power CO2 laser is used for organic materials such as polymers, rubber, silicone, wood, cardboard, paper etc. because of higher absorptivity of the beam with these materials. Similarly, a fibre laser is used for cutting and etching of metals like iron, steel, copper, brass, aluminium etc. due to higher absorptivity of the laser beam with these materials.
Lasers have already replaced many traditional machining techniques and their applications are increasing in areas like welding, bending, and surface hardening. In short, laser is a one point solution to many manufacturing processes and will soon replace many traditional techniques.